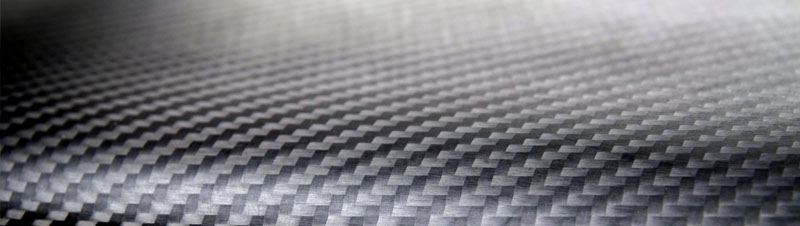
A no-contact heating tool for shaping and heating complex parts for the aerospace sector.
The aerospace industry makes frequent use of composites in structural applications and components, because of their versatility. However, the new-generation composite technology, like PEEK, requires temperatures exceeding 400°C for curing and shaping.
For some products, aircraft manufacturers are looking for solutions that don’t require the use of an autoclave, which is an expensive procedure.
Themocoax has come up with a heating tool that takes the shape of complex parts to be moulded and heats them. Our heating element enables manufacturers to shape the carbon fibres without breaking them.
No-contact Heating Tool for PEEK manufacturers
Manufacturing plants that make parts for the aerospace industry will welcome the time and money saving benefits of the heating tool designed by Thermocoax. The heating tools are also useful for maintenance companies needing to repair PEEK parts.
The normal procedure for shaping and moulding composites is to use an autoclave. This oven removes the air from the resins. However, it is extremely expensive and there is a risk that the materials will bubble and break.
A no-contact device to fit complex 3D shapes
The heating tool engineered by Thermocoax is a no-contact device based on mineral insulated cabling produced in house. With a rapid increase in temperature, the heating element joins and welds composite plastics at 100 kWatt under 400 V with 4 loops of heaters, for instance. Attached to a specially designed support, the cable reaches the infrared range and will fit complex 3D shapes.
The heating elements are embedded in the tooling, which means no dust, therefore no cleaning, and no friction and no burring, therefore no dusting or deburring. Electrical connections are equipped with true cold ends, so there are no limit as regards cable bending position.
A leading name in heating tools
Thermocoax has a wealth of experience in producing heating tools for general and automotive industry, based on their mineral insulated cable produced in house. This heating technology has the benefit of being fast and therefore highly productive.
The cost and time savings for manufacturers are therefore significant.
Heating Tools : Technical Data
- Heating moulds up to 450°C
- Best homogeneity +/- 2°C
- Cable diameter down to 1 mm for high homogeneity
- Cable diameter up to 5 mm for high power
For more information about Thermocoax heating solutions for composite technology, please don’t hesitate to request a quote.